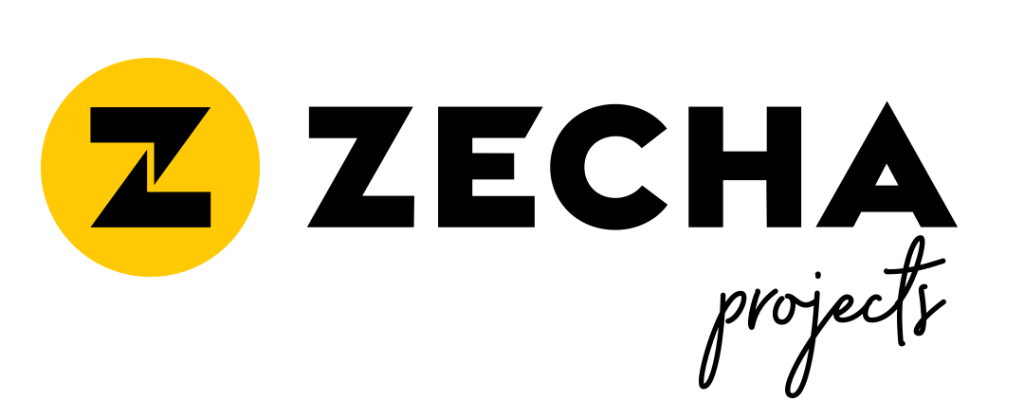
Pioneering Research Projects by ZECHA
Discover how ZECHA Hartmetall-Werkzeugfabrikation GmbH is revolutionizing the world of precision tool manufacturing through groundbreaking research projects. From the innovative cryogenic cooling techniques in titanium milling to the advanced surface finishing methods in the SQUISH project, ZECHA’s contributions are setting new standards in efficiency and quality. Explore these cutting-edge projects and learn how ZECHA’s expertise is driving advancements in tool technology and production processes.
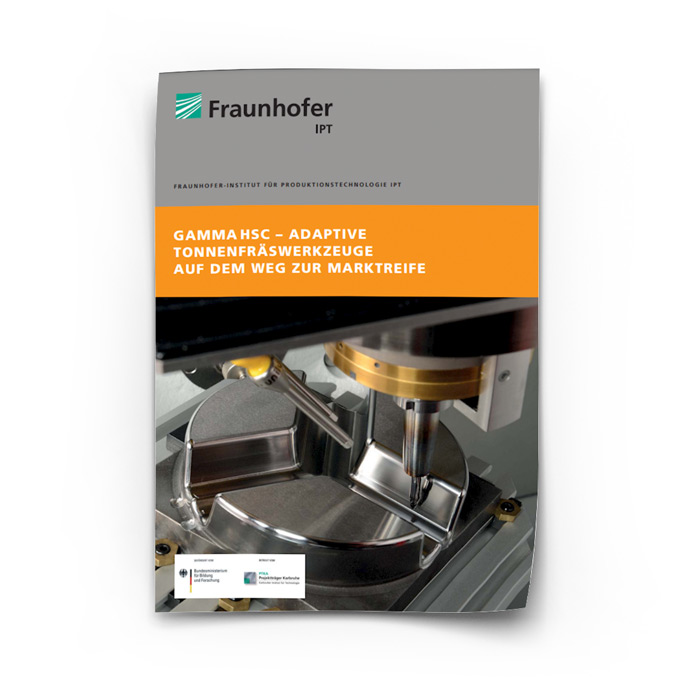
GAMMA HSC
Enhancing Productivity and Surface Quality with Adaptive Milling Tools
ZECHA Hartmetall-Werkzeugfabrikation GmbH has been a key contributor to the GammaHSC project, which focuses on the development of adaptive barrel milling tools designed to accelerate milling processes and improve surface quality. This research, organized by the Fraunhofer Institute for Production Technology (IPT) and funded by the German Federal Ministry of Education and Research (BMBF), aims to integrate advanced tool geometries into commercial CAM systems for efficient and error-free machining. ZECHA’s role involved the precise manufacturing of these innovative tools, leveraging their extensive experience and cutting-edge technology. The new barrel milling tools have demonstrated significant improvements in productivity and surface finish, particularly for large-scale forming tools and injection molds. For a comprehensive overview of the GammaHSC project and ZECHA’s involvement, download the full report by clicking the button below.
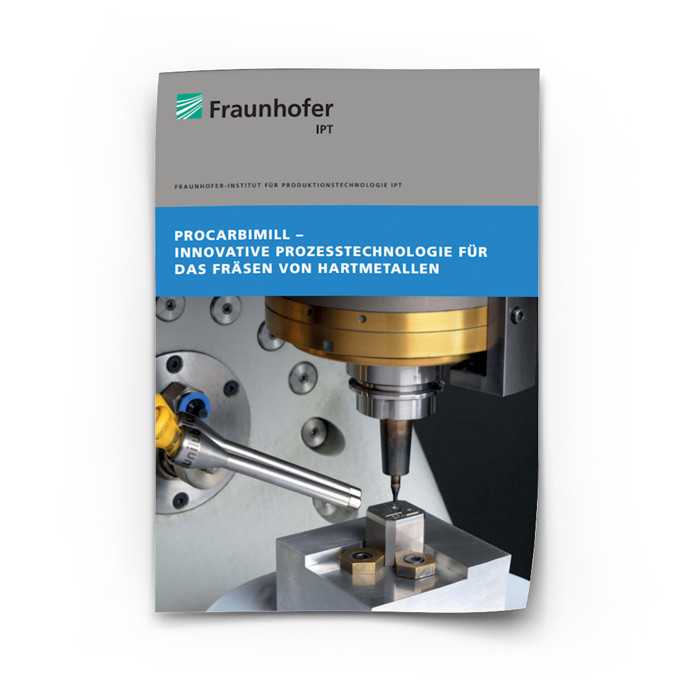
PROCARBIMILL
ZECHA’s Pivotal Role in
Carbide Milling Research
ZECHA Hartmetall-Werkzeugfabrikation GmbH played a pivotal role in the ProCarbiMill project, bringing their extensive expertise in the manufacturing of high-performance carbide milling tools. Organized by the Institute for Production Management (Frauenhofer Institute), Technology, and Machine Tools (PTW) at the Technical University of Darmstadt, this study aimed to enhance milling technologies for carbide materials. ZECHA’s contributions were essential in adapting the production processes to significantly extend tool life. Their involvement included the development and conditioning of diamond-coated milling tools, achieving reproducible precision for tools ranging from 0.5 mm to 6 mm in diameter. The insights gained from this project are poised to serve as a foundation for future tool series and innovations in milling technology. To delve deeper into the specifics of the ProCarbiMill project and ZECHA’s contributions, download the full report by clicking the button below.

Cryogenic Cooling Innovations in Titanium Milling
Enhancing Tool Life and Efficiency with ZECHA’s Advanced Technologies
ZECHA Hartmetall-Werkzeugfabrikation GmbH has been at the forefront of an innovative research project focusing on the milling of titanium alloys using cryogenic cooling techniques. This project, organized by the PTW Institute at the Technical University of Darmstadt and supported by the AiF, aimed to address the significant wear challenges faced during titanium machining. ZECHA’s development of new VHM torus end mills optimized for cryogenic CO2 snow jet cooling demonstrated remarkable improvements in tool life and process efficiency. By reducing the temperature at the cutting edge and minimizing thermal stress, ZECHA’s tools significantly outperformed traditional methods, setting new benchmarks in titanium machining. For an in-depth look at this pioneering research and ZECHA’s contributions, download the full report by clicking the button below.
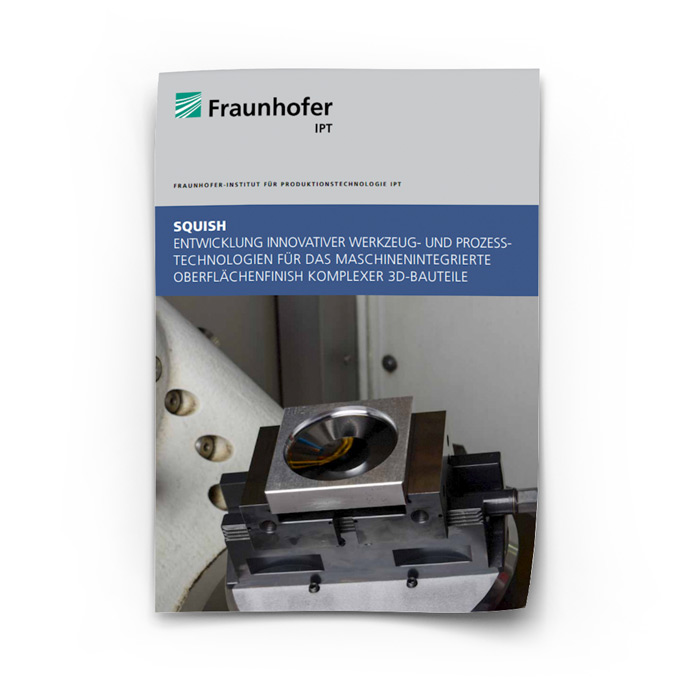
Innovative Surface Finishing with SQUISH Project
Reducing Surface Roughness and Polishing Time in Complex 3D Parts
ZECHA Hartmetall-Werkzeugfabrikation GmbH contributed significantly to the SQUISH project, which aimed to develop advanced tool and process technologies for integrated surface finishing of complex 3D parts. This research, organized by the Fraunhofer Institute for Production Technology (IPT) and supported by the German Federal Ministry of Education and Research (BMBF), introduced two innovative tool concepts—a diamond burnishing tool and a carbide ball-end tool with a large radius cutting edge. These tools effectively reduced surface roughness post-milling, thereby decreasing the duration of subsequent polishing processes. ZECHA’s expertise in precision tool manufacturing ensured the successful implementation of these tools, highlighting their role in enhancing production efficiency and surface quality. For a comprehensive understanding of the SQUISH project and ZECHA’s involvement, download the full report by clicking the button below .
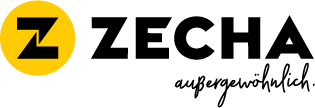
ZECHA Hartmetall-
Werkzeugfabrikation GmbH
Benzstraße 2
D-75203 Konigsbach-Stein
+49 7232 3022-0
info@zecha.de
Contact Page
Cutting Data Calculator